The Australian construction industry is one of the cornerstones of our economy, contributing significantly to GDP and employment. Yet, despite its importance, the sector faces a persistent challenge that threatens its sustainability: productivity stagnation. Compared to industries like manufacturing and finance, which have successfully harnessed technology to boost efficiency and outputs, the construction industry has fallen behind, particularly during the delivery phase of projects. A missed opportunity, especially given that labour costs alone account for 20–40% of total project expenses.
Fortunately, the solution is well within reach: leveraging mature and scalable technology platforms to improve efficiency during the construction phase.
A Snapshot of the Problem
The Australian construction industry is a significant economic driver, contributing approximately 7–9% to GDP and employing over 1.2 million people. However, research shows that the sector’s productivity has stagnated or declined over the past decade. While the pre-construction phase has seen impressive progress with tools like Building Information Modeling (BIM) and digital engineering platforms, the same cannot be said for the construction delivery phase.
For instance, industries like manufacturing have embraced automation, robotics, and real-time analytics, creating leaner processes that optimise outputs while reducing waste. In contrast, construction projects still experience delays, rework, and inefficiencies caused by outdated practices, poor communication, and a lack of team integration.
This productivity gap isn’t just a technical problem; it’s a financial one. Labour productivity is a critical component that directly impacts overall project costs. With labour accounting for up to 40% of expenses, any inefficiencies in this area can quickly escalate budgets, delay project timelines, and erode profit margins.
Technology as a Proven Enabler
The good news is that solutions already exist. The construction industry doesn’t need to invent new technologies—it just needs to adopt or adapt those proven effective in other sectors.
Take Building Information Modeling (BIM) as an example. BIM has revolutionised the pre-construction phase by providing a centralised digital model that integrates architectural, structural, and engineering designs. This allows for better collaboration, visualisation, and clash detection, reducing errors and rework during planning. Similarly, real-time data analytics, mobile applications, and project management platforms are readily available and can significantly enhance project execution during delivery.
The Construction Phase: An Untapped Opportunity
While technology adoption in pre-construction has been transformative, the construction phase—where the actual building takes place—relies heavily on traditional methods. Inefficiencies, including poor resource allocation, inadequate tracking, and fragmented stakeholder communication, plague this phase. The result? Delays, cost overruns, and frequent rework.
These challenges can be addressed by leveraging digital tools during construction. For example:
- Real-Time Monitoring: Mobile apps and IoT devices can provide live updates on project progress, equipment usage, and workforce deployment, ensuring that managers have a clear view of the site.
- Data-Driven Decision-Making: Real-time analytics platforms can identify bottlenecks, track material usage, and predict potential delays before they become critical issues.
- Collaboration Tools: Cloud-based platforms enable teams to stay aligned, reducing the communication breakdowns that often lead to errors.
- Automation: Drones, robotics, and autonomous equipment can speed up repetitive tasks, enhance safety, and reduce reliance on labour-intensive processes.
These technologies improve efficiency and increase visibility and accountability across teams. They allow managers to track real-time performance metrics, address problems proactively, and deliver projects on time and within budget.
Barriers to Adoption
If the benefits of technology in construction are so clear, why hasn’t the industry embraced it fully? The answer lies in a combination of cultural and structural challenges.
Firstly, the construction industry is traditionally risk-averse, with many stakeholders hesitant to adopt new technologies due to the upfront costs or fear of disrupting established workflows. Additionally, there’s often a lack of digital skills among the workforce, which can create resistance to change.
Furthermore, in many construction projects, there is a common practice of addressing on-site issues by simply adding additional labour to resolve them quickly. This reactive approach is often justified because labour costs are charged directly to the project’s budget rather than impacting administrative overheads. On the surface, this might seem like a practical and immediate solution to keep the project on schedule. However, this practice has significant downsides.
By relying on additional labor as a quick fix, construction teams often bypass the need to critically assess underlying inefficiencies or to explore innovative, long-term solutions. This approach can create a culture where productivity improvements and technological innovation are deprioritised, as the perceived urgency to “fix the issue now” outweighs the need to address the root causes of inefficiency.
Additionally, when projects remain within their overall budget despite these reactive measures, there’s little incentive to challenge the status quo or rethink how human and technological resources are utilised. Over time, this reliance on added labour to solve problems perpetuates inefficiencies, keeping productivity stagnant and leaving untapped opportunities for improvement unaddressed.
Actual progress comes from shifting the focus from temporary fixes to proactive strategies that drive productivity, optimise labour utilisation, and embed innovation into workflows. For example, leveraging real-time analytics and digital tools can help identify recurring issues early, enabling teams to develop smarter processes rather than defaulting to more human resources as the solution.
Finally, the fragmented nature of the industry, where projects frequently involve multiple contractors and subcontractors, makes standardising processes difficult.
However, these barriers are not insurmountable. The technologies needed to drive improvement are mature, scalable, and readily accessible. With the proper training, change management strategies, and leadership, construction firms can overcome these hurdles and position themselves for success.
The Case for Sustainable Productivity
Sustainable productivity improvement in construction isn’t just about keeping up with other industries—it’s about future-proofing the sector. As demand for infrastructure grows and skilled labour shortages become more acute, adopting technology becomes essential to meeting these challenges.
What’s more, the impact of these improvements extends beyond financial benefits. Greater efficiency leads to shorter project timelines, reducing construction activity’s environmental footprint. Enhanced safety measures through automation and monitoring technologies create safer worksites. And ultimately, better collaboration and fewer errors lead to higher-quality outcomes for clients.
Looking Ahead
The Australian construction industry stands at a crossroads. The tools needed to boost productivity during the construction phase are already available, and their potential to transform the sector is immense.
By adopting digital platforms, automating repetitive tasks, and using real-time analytics to drive decision-making, construction firms can reduce costs and deliver projects with greater precision and speed. The result will be a more resilient, competitive industry ready to meet the demands of a growing population and economy.
Technology enablement isn’t a luxury. It’s a necessity. The question isn’t whether the construction industry can afford to invest in these tools but whether it can afford not.
- Australian Bureau of Statistics. (2012). Australian National Accounts: National Income, Expenditure and Product.
- Australian Bureau of Statistics. (2023). Labour Force, Australia.
- McKinsey & Company. (2014). The construction productivity imperative.
- McKinsey & Company. (2017). Reinventing construction through a productivity revolution.
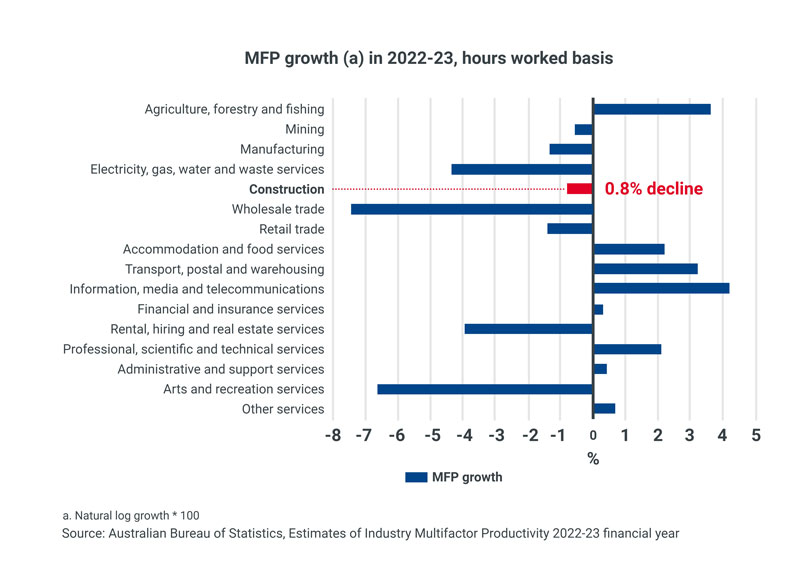
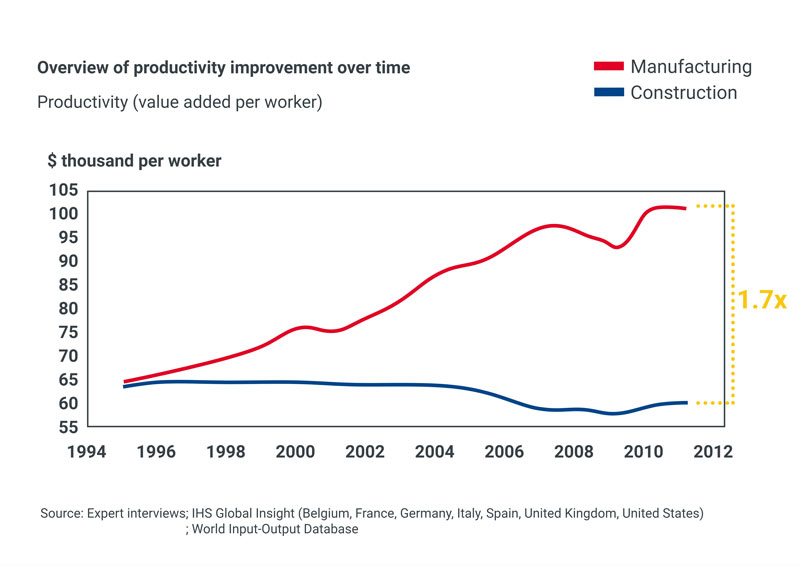
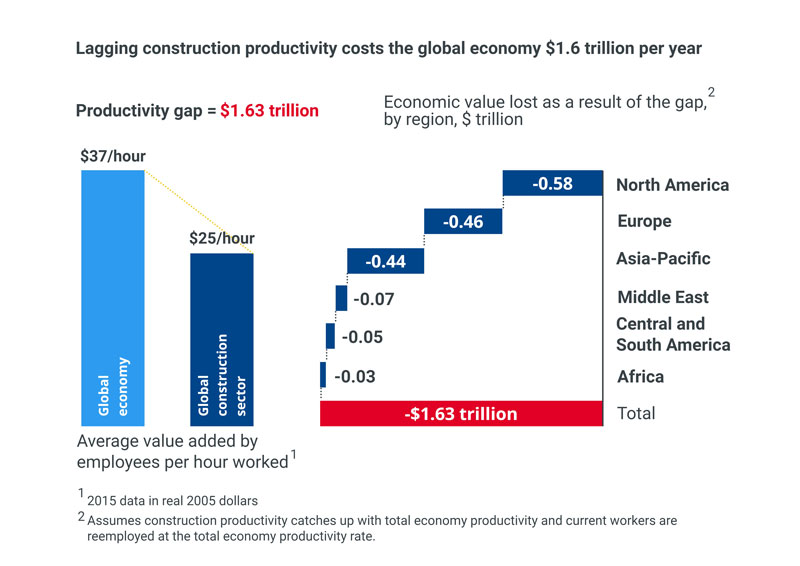